<FILE 01>
Deconstructing the notion of 'permanence' requires us to completely rethink our relationship with physical structures and systems, including schools, office buildings, entire cities, energy infrastructure, and homes.
The average lifespan of a building ranges anywhere from 30 to 50 years to hundreds of years (e.g., cathedrals, churches, and government buildings) depending on the materials used during construction. For example, U.S. school buildings are 45 years old on average. These problems disproportionately affect poor communities – as with most issues tied to inadequate funding in these areas. In older cities, schools average closer to 60 to 70 years old. However, problems associated with inadequate school buildings are not exclusive to high-poverty cities. There have been reports that some schools in the most affluent areas in the country had malfunctioning boilers during cold seasons.
Electricity generation from commercial nuclear power plants in the United States began in 1958. At the end of 2021, the United States had 93 operating commercial nuclear reactors at 55 nuclear power plants in 28 states. The average age of these nuclear reactors is about 40 years old.
And as we saw with the onset of COVID-19, large cities with dense office buildings were decimated financially given the absence of employees and have still struggled to attract new tenants.
So what about all of those empty office buildings?
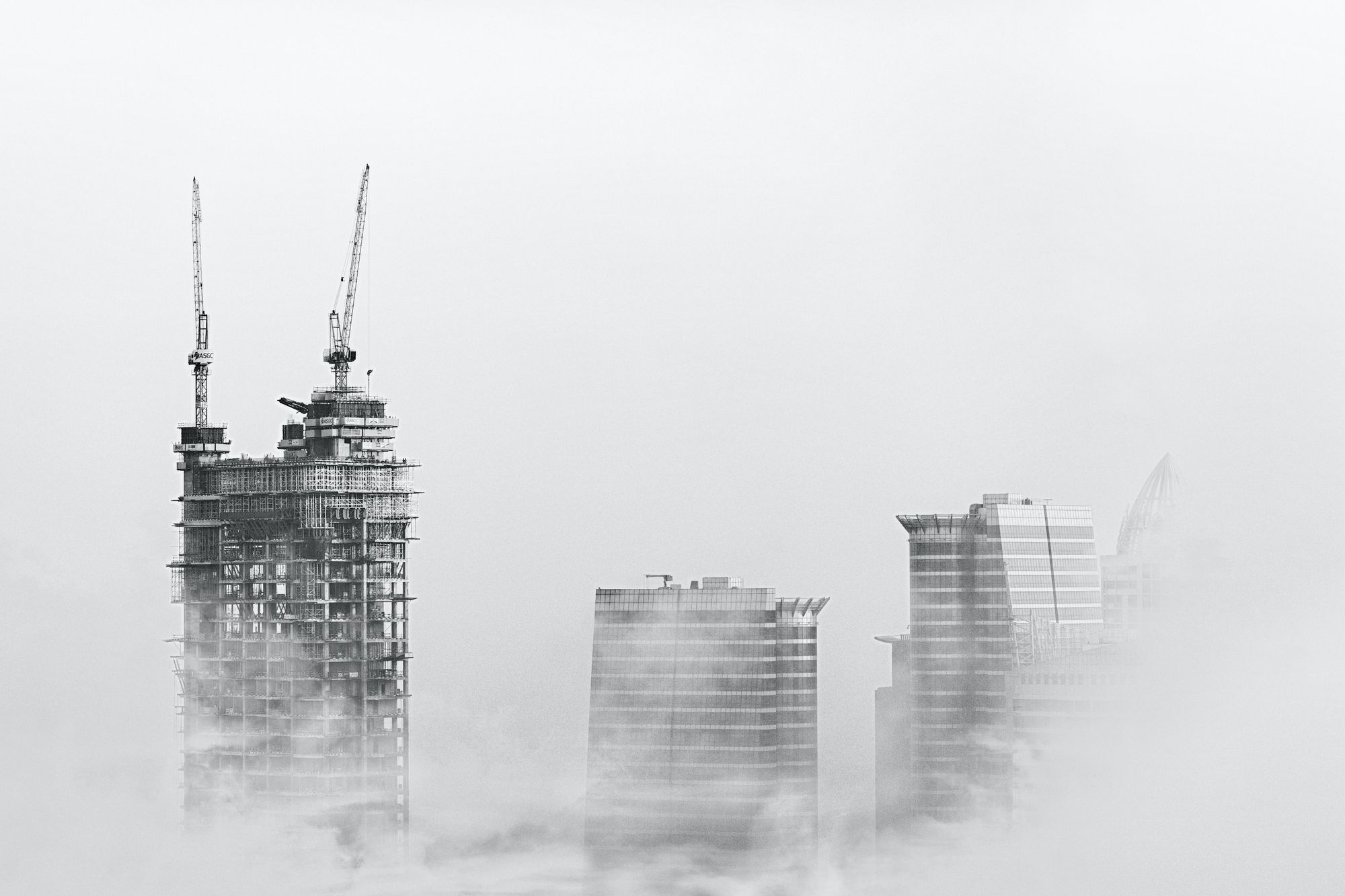
“Over the next few years, as tenants start to rethink space needs and their leases rollover, they’ll go into better buildings, and the [worse] buildings will be in trouble.” - Joseph Gyourko, Wharton real estate professor
New York City is already looking into converting 10% of Midtown's less-desirable "Class B" commercial buildings into apartments – with one study estimating the city could create ~14,000 apartments from unused commercial office space. And despite America's largest cities seeing the sharpest pandemic year population losses during COVID-19 – the 2020 Census shows that, when looking at the 2010-2020 decade, many major cities grew faster than the previous decade and most registered increased racial diversity. Though converting less-desirable empty commercial buildings is a good place to start, we can already see how the 'permanence' of these many physical structures leaves us with the inability to effectively and dynamically adapt with these rapid shifts in migration and lifestyle preferences.
The Benefits of Interoperability & Modularity
The architect David Wallance, in his book The Future of Modular Architecture, introduces the idea of moving away from 'permanence' and bespoke builds to a more interoperable and modular approach of building physical structures that relies instead on a new 'industrial-scale system'. This next-generation system for mid-and high-rise modular architecture would be an open-source modular system derived from the standard dimensions of intermodal shipping units.
Why intermodal shipping units? It allows for a smooth transition into leveraging existing intermodal freight transport systems and global supply chains to create a highly-efficient, well-designed, and affordable industrial product that can be manufactured and distributed at scale with our legacy infrastructure. What could we do with this level of optimization in architecture and construction? In the summer of 2021, China's Broad Group was able to assemble a 10-story residential high-rise in just over a single day – or 28 hours and 45 minutes, to be exact. Ok, but is it even safe and practical? According to Broad Group, the modular building is durable, earthquake-resistant, and can be dismantled and moved if needed.
Now, a clear and obvious tension between standardization and individualism will naturally occur but we must ensure that we standardize enough to benefit from the cost-effective production on an industrial scale, while remaining flexible enough to meet the needs of hyperlocal markets with unique permitting requirements, climate considerations, and personal preferences. But Wallance wants to take this idea even further beyond just simply standardizing and making efficient the manufacturing and distribution of 'intermodal modular architecture'.
“I believe in a paradigm shift. This paradigm shift is more than just modular construction. Modular architecture has been around for over fifty years; it isn’t new. The paradigm shift I put forward is an open-source kit-of-parts-based system, spurring the collaborative growth of new ideas within a baseline framework, similar to how apps are developed that plug into a smartphone operating system. I believe in flexibility within standards. The smartphone operating system is a set of technical standards produced on an industrial scale, which is simultaneously open enough that third party app developers can do anything that they can dream of, as long as it plugs in seamlessly with the technology. I believe that intermodal modular architecture can bring this approach to cities globally. With the right incentives, architects, industrial designers, product developers, and anybody who has the wherewithal to come up with an idea and get it manufactured can plug into the intermodal system, to create almost anything.” - David Wallance
We are already beginning to see a real and meaningful need for this 'open-source kit-of-parts-based' system emerge after the pandemic left many people stuck at home revaluating their relationship with their space. Some of the many adjustments people are already making to their homes and spaces include:
I believe that in the not too distant future there will even be entire architecture firms or companies completely dedicated to focusing on just one type of room or intermodal shipping unit instead of entire structures. There will be architecture firms or companies that only make 'plant rooms' or 'virtual-reality rooms' and instead iterate on several variations, layouts, and optimizations for these single verticals.
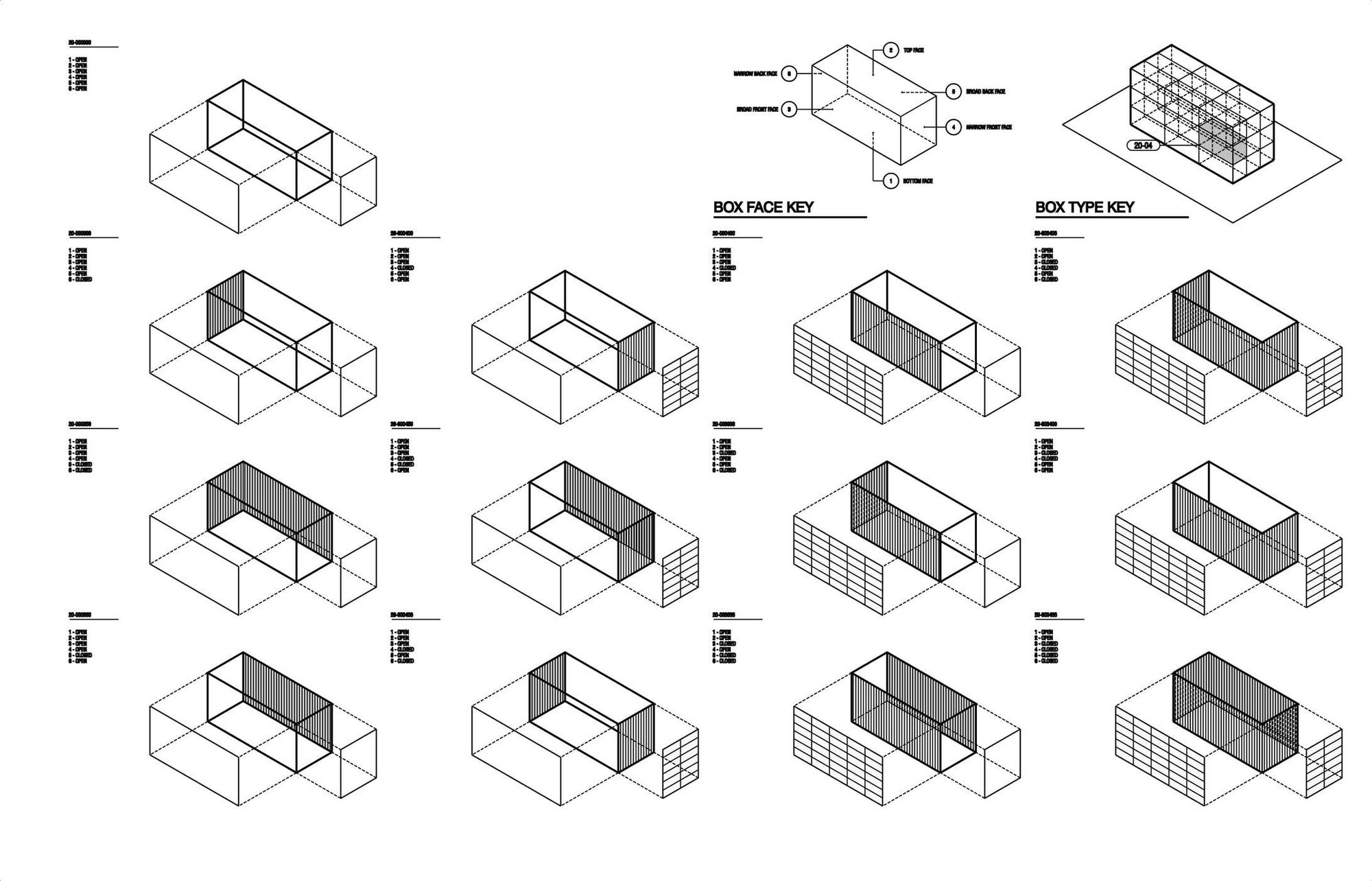
For the buildings and structures where intermodal shipping units are not practical or possible, innovative engineering techniques like 3D printing can be useful for streamlining production and cutting material and manufacturing costs alongside emissions.
You can also reduce emissions by using less cement & focusing instead on reinforcing slabs along their principal ‘stress lines’ by optimizing the internal geometry of the cement & then filling the rest of the space w/ 3-D printed recyclable mineral foam.https://t.co/LAHrioU6dC
— Eddy Medina (@eddyamedina) April 9, 2022
What about for structures that are already built? How can they become more energy efficient, dynamic, and adaptive? A German renovation firm – Ecoworks – is able to make old buildings energy efficient simply by taking a 3D scan of a house, prefabricating wood panels of identical shape and scale to be attached to the outside, and ultimately turning these inefficient buildings in Germany into net-energy producers. The panels they make come with built in solar panels and insulation, meaning they can be installed on the host building in as little as 20 minutes. They’re made from wood that’s been harvested after its achieved optimal carbon capture. Ecoworks was able to make an apartment block built in the 1930s so inexpensive to heat, cool, and power, that the solar panels on the roof made it a carbon-negative building.
We can see a lot of similarities from intermodal modular architecture present in advanced small modular reactor (SMR) nuclear technology and other promising climate tech innovations. According to Dr. Jessica Lovering (Co-Founder and Co-Executive Director at the Good Energy Collective), SMRs can be built more like a commercial product with standardization and assembly line manufactured components taking advantage of the economics of factory production. And SMRs are built using 'passive safety' features that rely on the natural laws of physics to maintain their structural integrity – making them far more viable than large legacy nuclear power plants that also have to rely on complex engineered systems to operate.
Take Radiant Nuclear as an example. Radiant is innovating on the best of SMR technology while also designing a product that is practical. Do you recognize the shape of their 1 MegaWatt (MW) reactor below? Radiant has developed a compact, portable, low-cost 1MW micro-reactor (i.e., a subset of SMRs designed to generate electrical power typically up to 10 MW) that fits in a...you guessed it...intermodal shipping unit, can power about 1,000 homes for up to 8 years, and uses a helium coolant instead of water. The use cases for a zero-emission nuclear microreactor that can plug seamlessly into existing intermodal freight transport systems and global supply chains include: providing electricity and heat to remote communities, disaster areas, and bases.
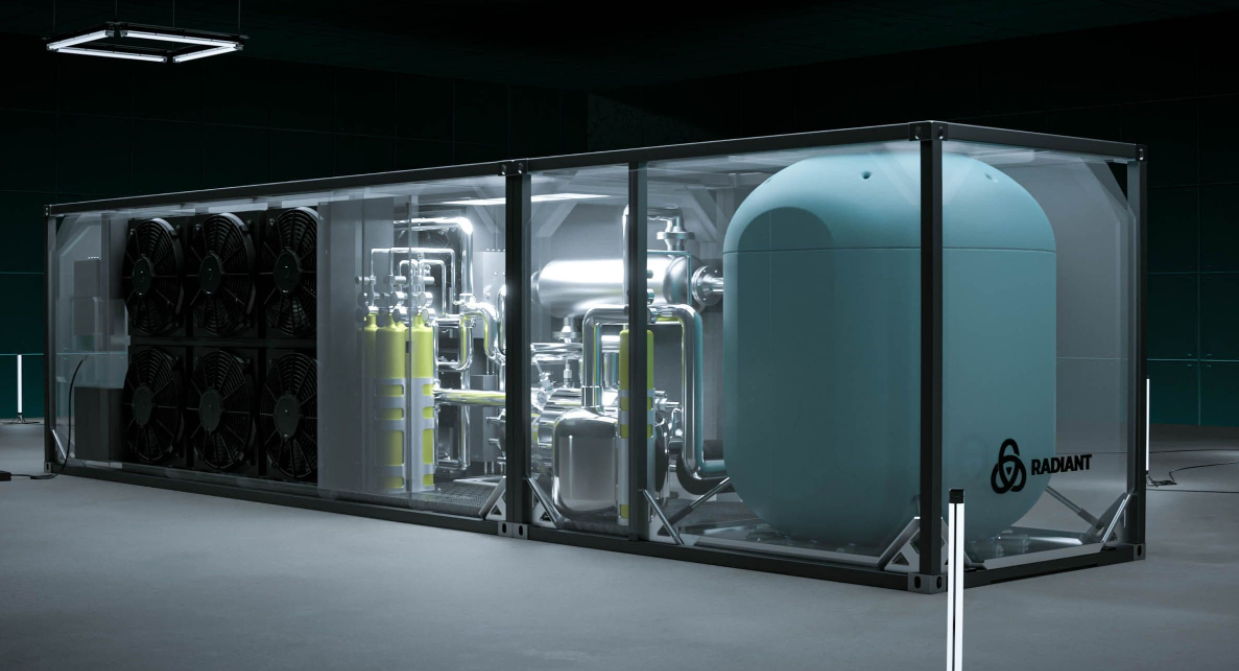
There is a clear and obvious need for us to rethink the notion of 'permanence' as it relates to our housing, cities, and energy systems. As the world rapidly changes post-pandemic and as the impacts of climate change continue to shape communities – it will become increasingly essential to dynamically adapt our physical structures and energy resources to best fit our needs.
Further Research
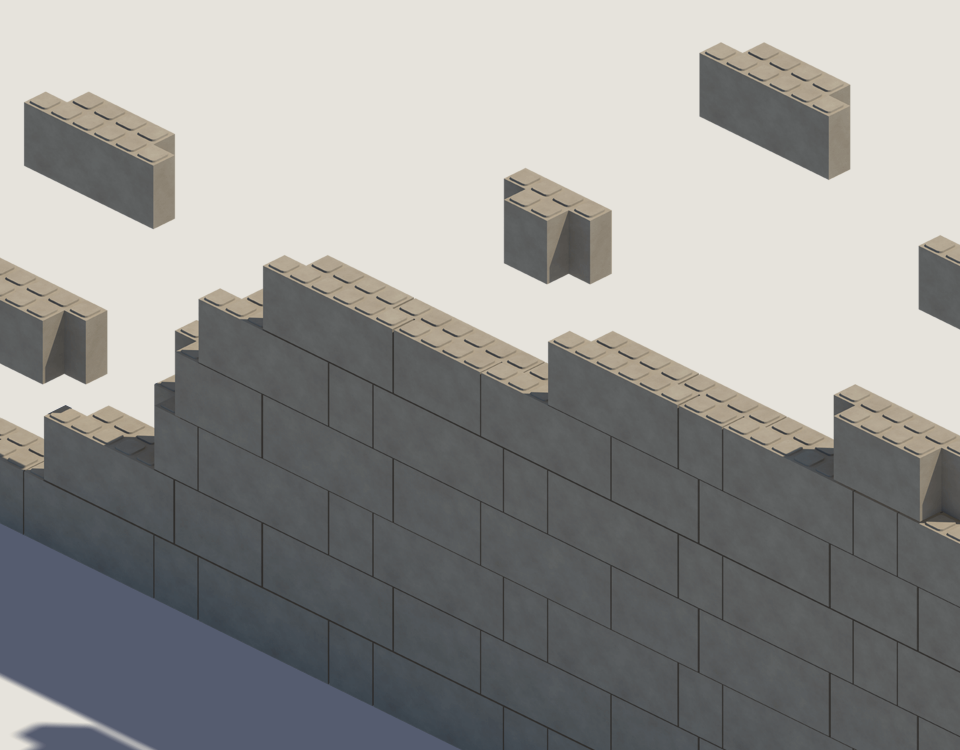
ImpactFuture Lab content is for informational and educational purposes only and is not intended to provide specific advice or recommendations for any individual/organization or on any specific security or investment product. The content on this site are of my own opinions and do not represent the positions, strategies or opinions of my Firm or its employees.